Traditional volume
based cost system (Direct labour hours/ Machine hours)
Do not recognize
the following:
- Additional set-up,
clean-up, scrap etc. related to more unique, complex, smaller products
Traditional ABC
maybe as good as Time driver ABC. But
- Relies on employee
estimates (lack of accuracy)
- Gives no recognition of
excess capacity (included in cost driver rates)
- Expensive to set up +
update
Problem 1
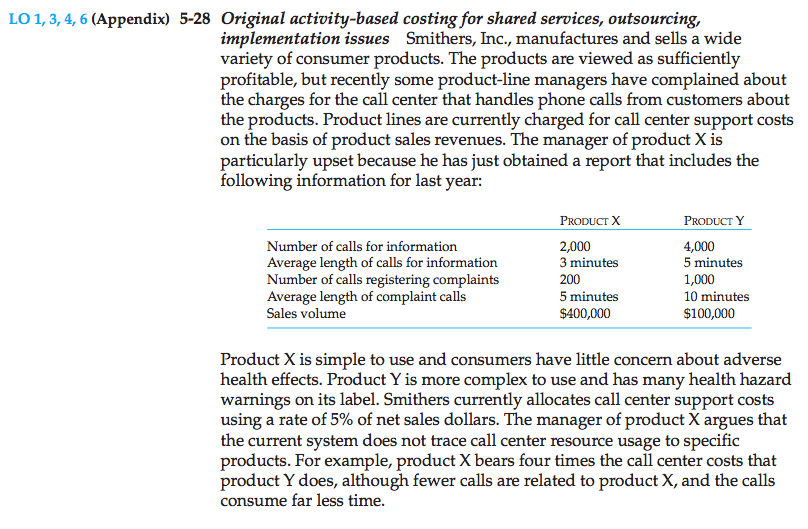
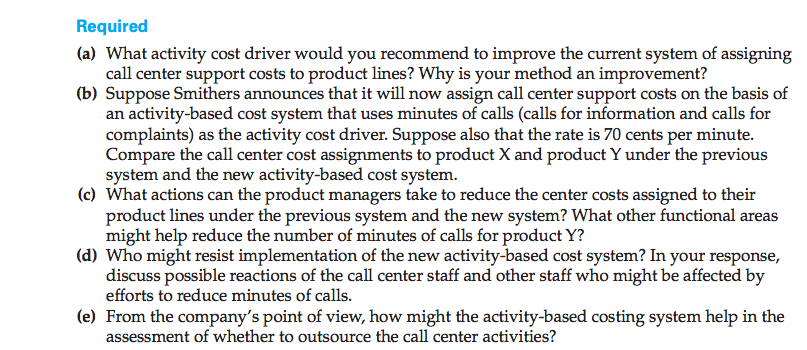
- Number of calls
per product (simple.
Number
of minutes of calls (duration cost driver)
- Provide better linkage to
costs
-
|
X
|
Y
|
Previous
(5% of sales)
|
20K
|
5K
|
Activity
based (.70 per minute)
|
4.9K
|
21K
|
- Previous system:
reduce allocation would be reduce sales
- This is counter productive
New
system: managers can find out methods to improve the system with other
functional areas of the company.
- People who would
resist:
- Manager of product Y
- Now we can see that most
of the resources are allocated to Y
- Stuck with more costs and
more work to minimize costs
- Fear of call
centers to be outsourced. Push call center staff to improve efficiency
and lower costs per minute.
Problem 2
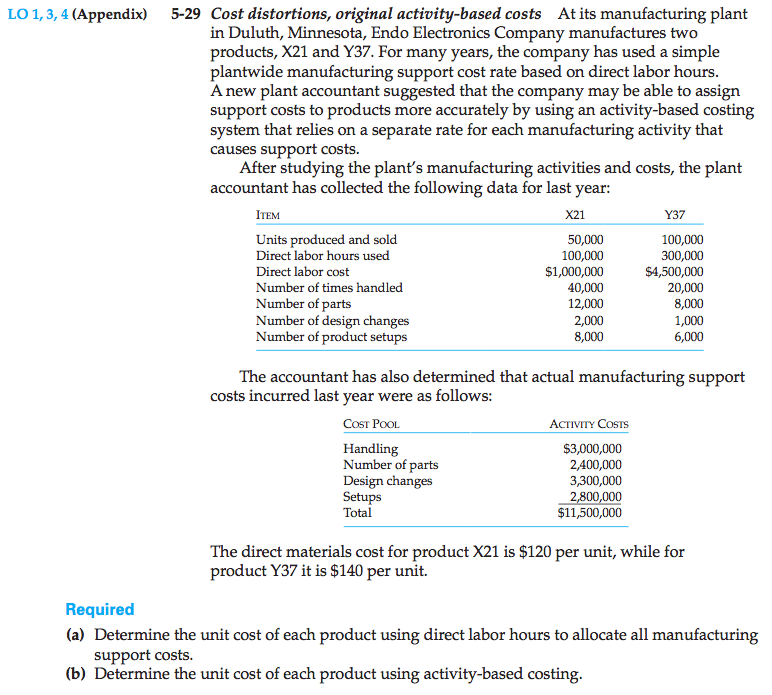

- M support cost
driver rate = 28.75/labour hour
|
X21
|
Y37
|
Direct Materials
Cost
|
120
|
140
|
Direct labour
cost
|
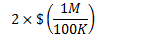
= 20
|
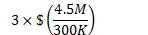
45
|
M support cost
|
57.5
|
85.25
|
Unit cost
|
197.50
|
271.25
|
-
|
X21
|
Y37
|
Unit cost
|
284.80
|
227.60
|
- Provides a
better cost/effect relationship
- Endo should
consider raising X21's price and lowering Y37's price. Right now the
price set for X21 produces a loss based on the activity-based costing
- The company can
explore ways to reduce design changes and the number of parts for X21
since it has twice as many design changes and 50% more parts compared to
Y37.
Management
should use collective efforts to reduce costs.
Problem 3
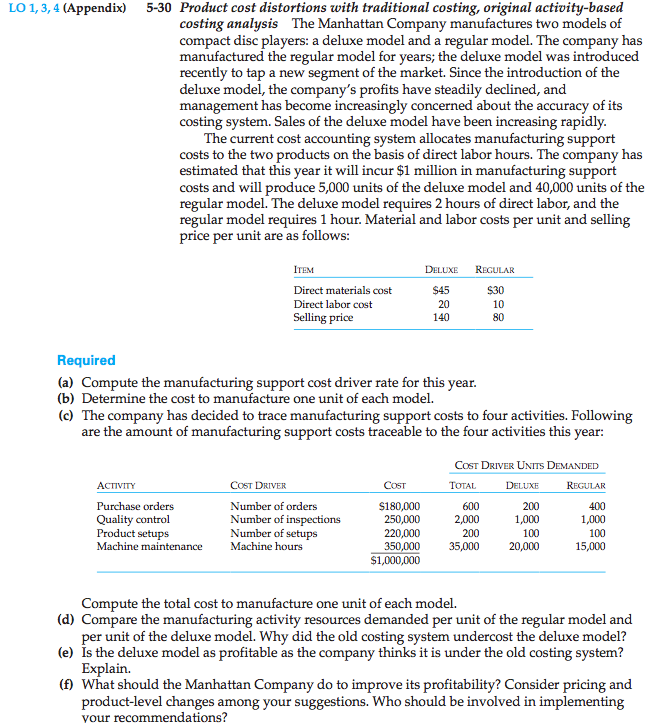
|